BRIDGE CABLES.
CL BRIDGE.
Lightweight CFRP cables/tension members/hangers in the context of bridge infrastructure present significant opportunities for improved sustainability, increased lifespans and reduced service demands. Subsequently, a considerable savings potential can be seen both ecologically and economically. These efficiencies can be seen primarily in network arch bridges of medium and large spans, with a specific focus on railway and road bridges that are highly loaded with heavy freight traffic.
Recently implemented on the first bridge to be fully suspended on carbon hangers [Stadtbahnbrücke], Carbo-Link’s CL BRIDGE cables passed a number of tests to simulate active life spans of 100 years. Cyclical load tests between 18 and 23 million were passed with negligible changes in residual strength; proof of fatigue resistance ensuring stability, operational efficiency and traffic safety.
Carbo-Link’s CL BRIDGE cable/tension member/ hanger is based on proven carbon loop technology. Prepreg carbon tapes embedded with a toughened resin matrix are continuously wound around end fittings, either metal or carbon, to form a continuous loop, before consolidation into a round or shaped cable. All prepreg tapes are made in-house at Carbo-Link with Aerospace approved processes, ensuring perfect fibre alignment and prepreg tape tension. The process is flexible and adaptable meaning any raw material and resin matrix system can be used to produce the prepgreg tapes based on project specific requirements.
PROVEN COST REDUCTIONS.
Structural optimization enables direct material and cost savings in the CL BRIDGE cables themselves, and also in the primary structure due to improved load-bearing effect.
Material substitution from steel to CFRP has a multiplier effect through resource efficiency and increased sustainability of an entire structure.
Added value.
-
Dimensions driven by maximum tensile force
Utilize extremely high strength of the material
Cross-section is around 20% of the area compared to the steel
-
Strength driven design = reduction in associated stiffness
Equalization of forces = no asymmetrical loading across the structure
Low deformations under heavy traffic loads
-
No vibration due to higher natural oscillation frequencies
Simple & safe assembly: unit weight 30>60 kg vs 1’000>2’000 kg
Significant reductions in installation time with limited machinery
-
No corrosion from environmental conditions
Heavily resistant to chafe, impact & human influence
Fire resistance expectations exceed traditional materials
-
Visual inspections indicate cable health
No fatigue = long service life
Possible to NDT onsite if required
-
Simple & efficient installation processes
Long service life with no replacement schedule
Small cross-section & low EA = cost competitive material requirements
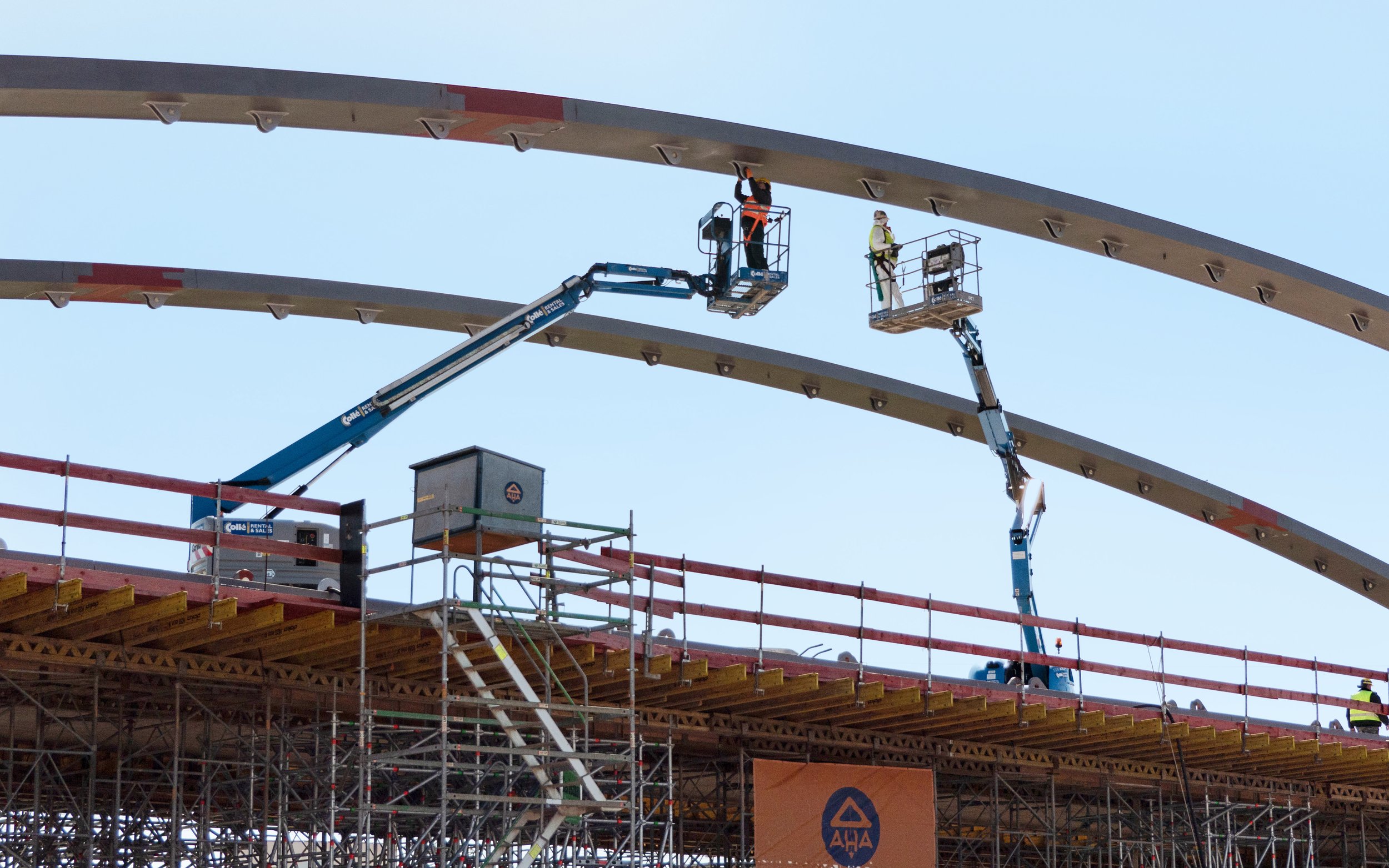
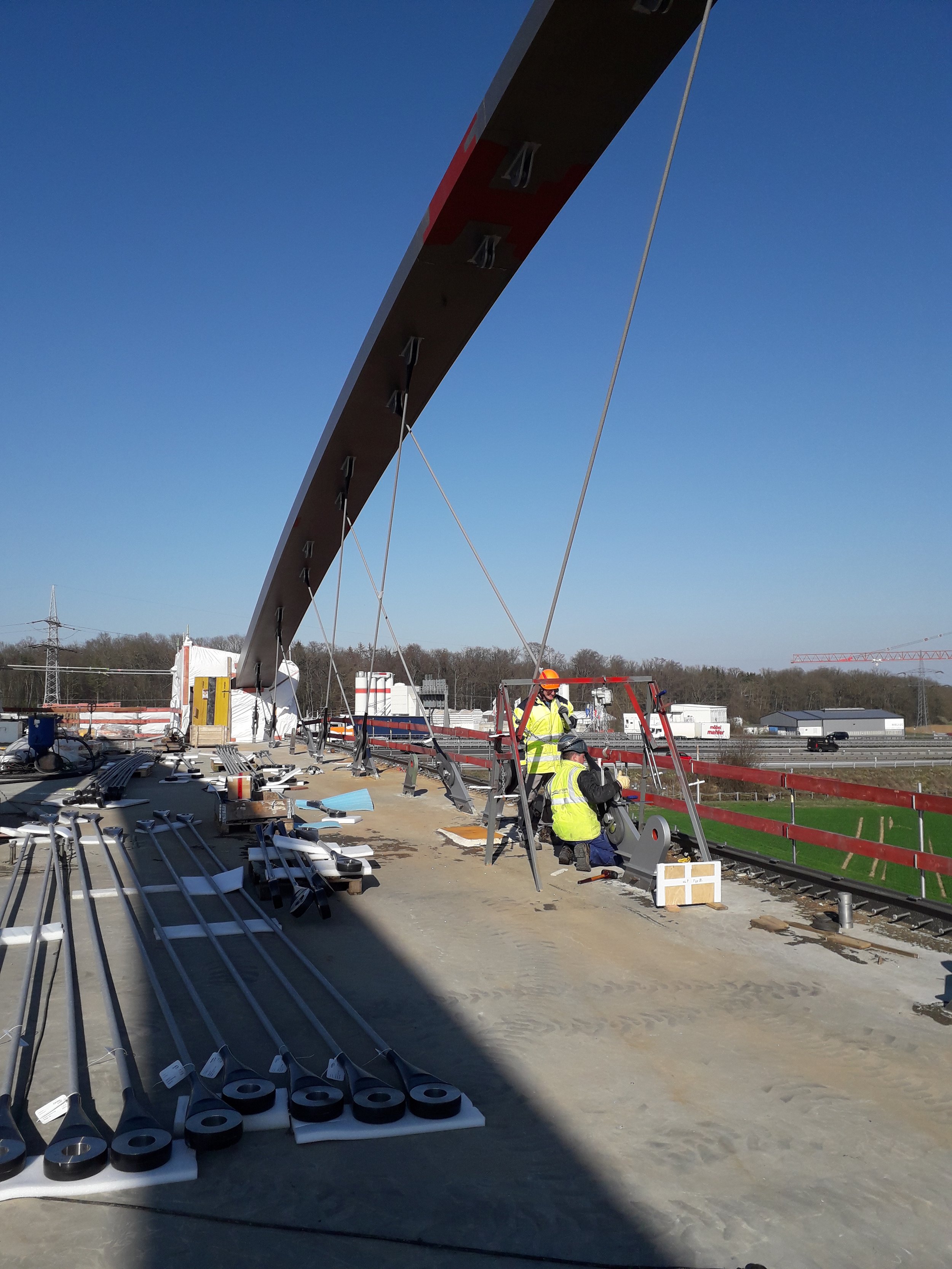
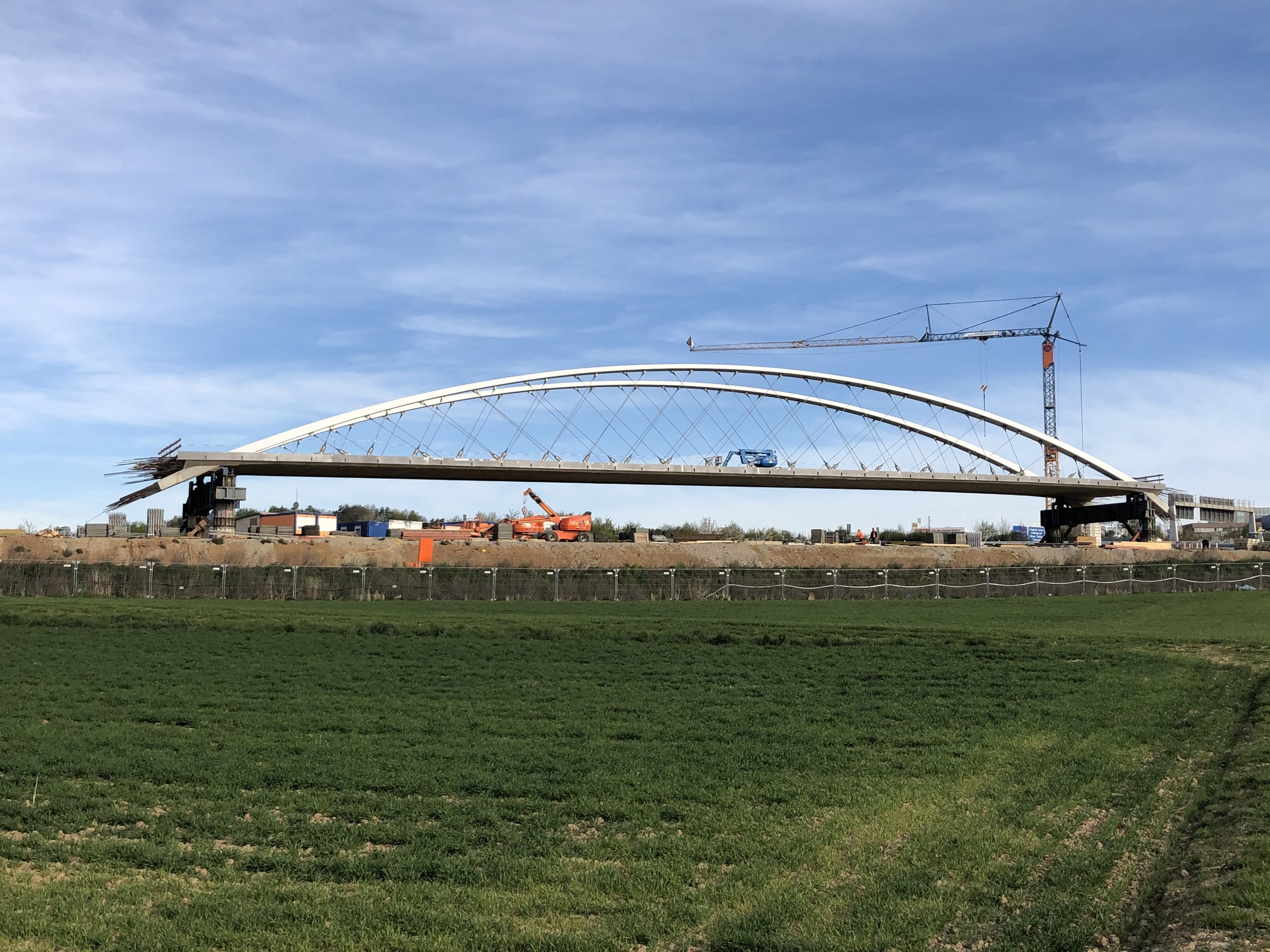
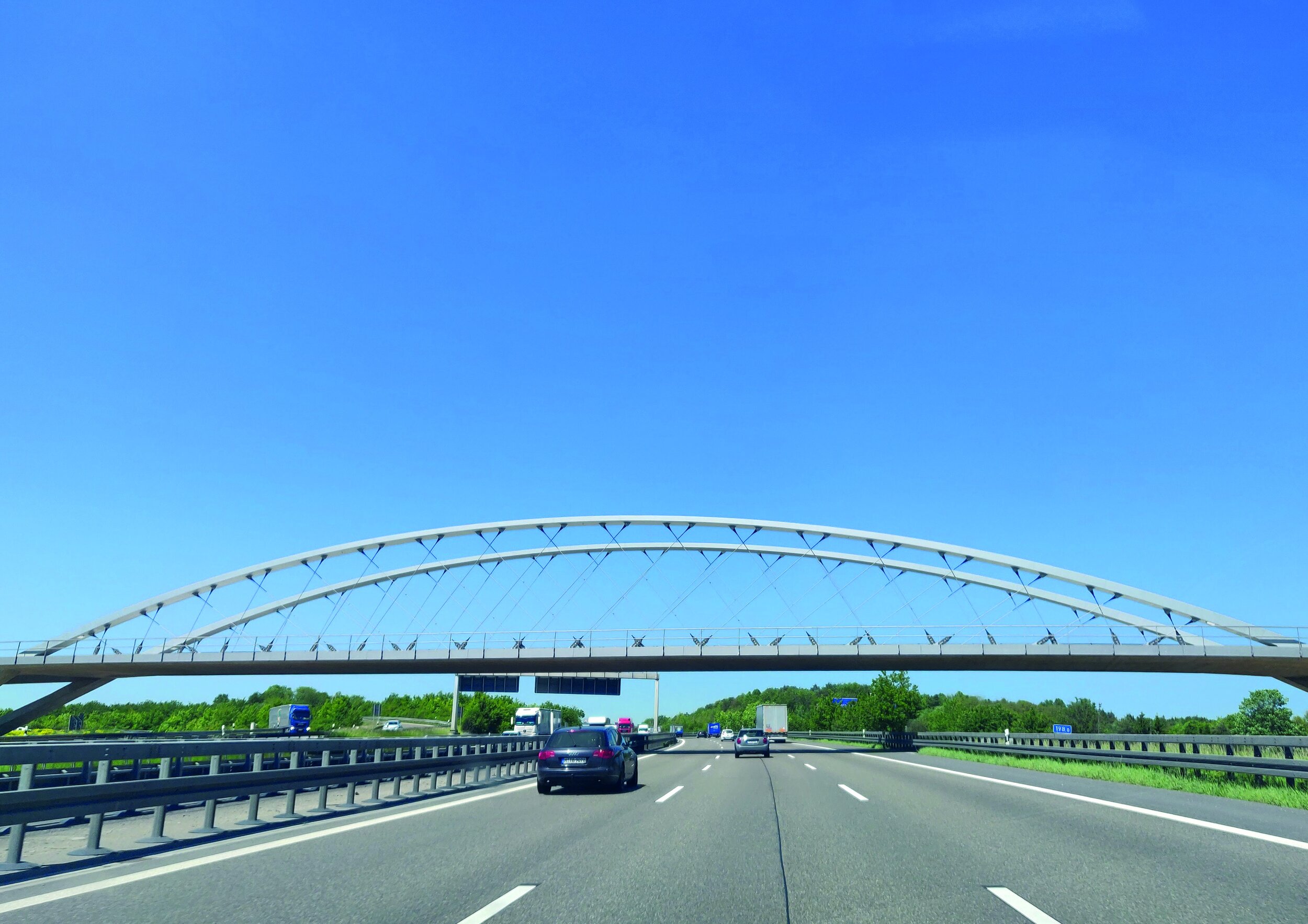
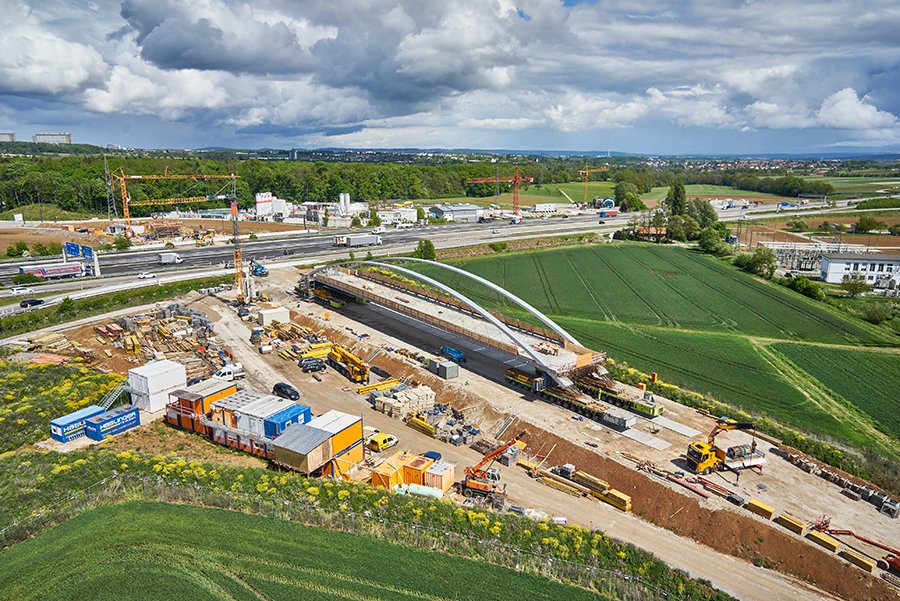
Further products & solutions.